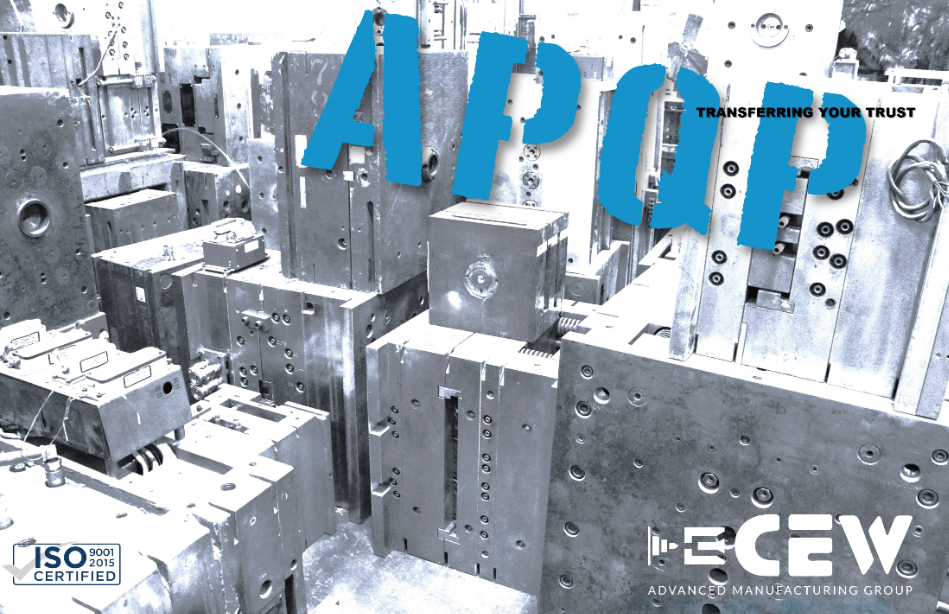
Recently, our Reynosa Mexico operations group, along with our engineering and quality teams partnered with one of the world’s leading manufacturer vision systems for the transportation industry. The scope of the project was to meet or exceed a highly accelerated timeline of ten days… including inspecting the tools, prepare the tools for production, sample the tools and submit the PPAP to the customer to start production for all 12 tools in the package…with the goal of delivering production volume in less than forty-five days. The team was given the challenge for all 12 tools to make and qualify 19 unique parts and get them into production in just a few weeks. The team also faced end-of-year production demands from our other OEMs, while balancing logistic and component scarcities in the mist of our December holiday shutdown.
CEW’s Advantage over our competitors centers on our process ability to quickly understand end customer requirements and then set and align on milestone-driven deliverables and expectations across cross-functional teams. To accomplish this fast-tracked project, our team utilized and leveraged our APQP process…“Advanced Product Quality Plan”. This framework and methodology are used by nearly all leading manufacturers in the Automotive, Heavy Equipment and Vehicle industries to ensure product quality, reliability and most importantly, consistent repeatability. Our APQP process installs confidence in our customers that we will meet their requirements and expectations this time…and every time!
Upon the tool’s arrival, CEW’s Advanced Manufacturing Group and our certified quality team inspected, measured, and calibrated each mold to ensure each arrived safely and in good condition. This review process also included fully measuring and calibrating each tool, its geometry, and ensured the associated components were all in good, working shape.
After this initial review, our AMG team proceeded with our rigorous, step-by-step validation testing. Depending on each part’s exact requirements, we utilized a series of process steps and testing protocols to ensure and demonstrate that we will produce high-quality parts and meet or exceed product design expectations.
Upon finishing our APQP Validation Process, we provided all preproduction sampling to our customer for confirmation, verification, and approval. After revisiting and reviewing the raw material specification of each individual part number, we then sequenced, planned and ran production according to the OEM’s orders and demand schedule. Our sales team and customer service group working in parallel ensured all logistical and delivery methods were in place and ready to go.
This success story is just one of many in a long line of examples of how CEW approaches a unique challenge and based on our advanced engineering and materials know how, can deliver on our promises.
Consider CEW for housing and running your next injection molding project. For nearly fifty years, CEW has delivered high-quality, ISO certified, best-in-class plastic injection molding to make millions of parts used by leading OEMs around the world.
“Committing to our APQP process… more importantly, believing in the process is the thread that unified our team and channels them to meet the challenge and exceed our customer’s expectations” noted Edgar Yerena, CEW’s Chief Operating Officer.
More than transferring your molds… transferring your trust to a Molder that works for you!